Before the advent of precast concrete manholes, the access points for sewer and storm water systems were made using brick and mortar.
Masons would build the structure in place, which took time and great effort. With the introduction of precast concrete manholes, the structure is built offsite at a controlled facility and then shipped to the construction site.
The fully built manhole is lowered into place, connected to the pipes in the system and backfilled with dirt. What used to take days is now completed in a number of hours.
Each manhole is custom built to exacting standards by structural engineers. Once the details of the job are sent to the precast concrete plant, workers ready steel forms with the proper openings and build cages of iron to reinforce the concrete.
The metal form is moved to the concrete mixer, where a precise mix of concrete is poured into the form. The chemical reactions that make the cement harden give off heat. The forms are set aside and allowed to dry for at least 24 hours.
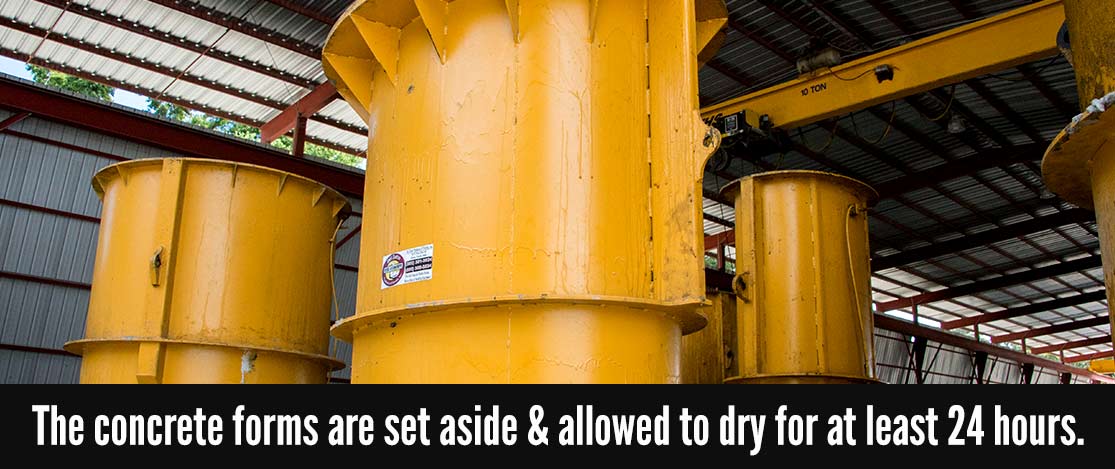
Non-stick Surface
Before the concrete is poured into the form, the walls of the form were thoroughly sprayed with oil to allow for an easier release.
When the forms are removed, the concrete manhole is still damp. Workers trim the excess concrete left behind and smooth out edges. The manhole is stamped with the job and client’s name and allowed to cure before it is shipped.
Del Zotto Products has been a pioneer in the precast concrete. Not only do we make precast concrete manholes and other products, but we also make the forms used to cast the products. We offer our forms for sale to other precasters and help them with technical advice. For information about our products or services contact us today.